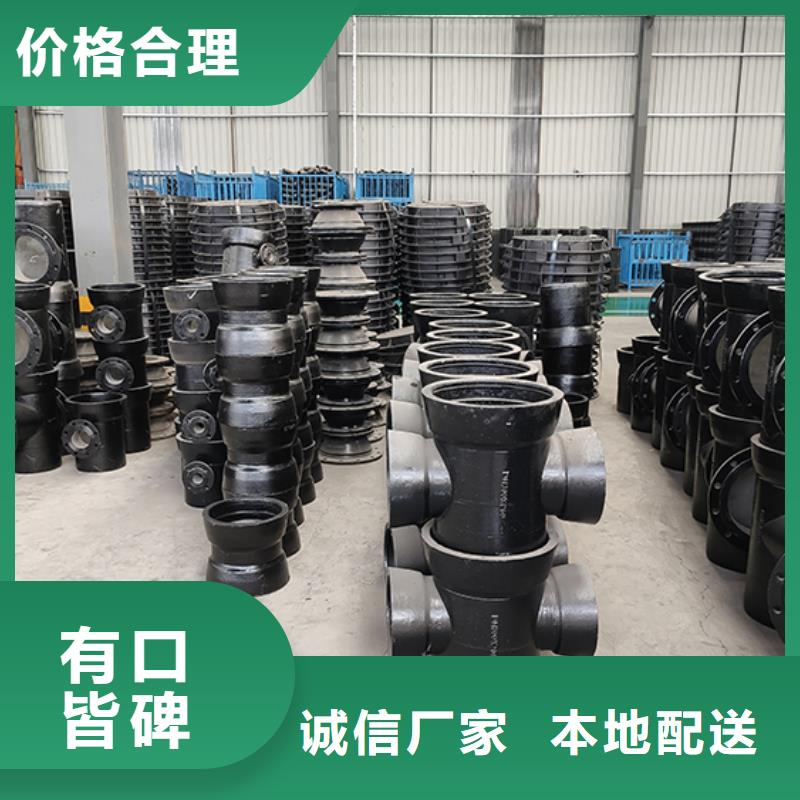
影响球墨铸铁管配件生产的7大因素: (1)碳当量:铁水碳当量过高(尤其是高硅含量),使石墨球化的影响。试验表明,厚壁铸件,当碳当量超过共晶成分是可能产生开花石墨。但增加的碳含量增加铁水镁回收率。因此,大多数高碳低硅生产的原则,通常硅含量在2%左右控制。此外,碳当量,铸件壁厚的选择:当管壁厚度为6.5?76毫米,碳当量的4.35%至4.7%;壁厚>76毫米,碳当量的4.3%到40.35%。 (2)硫:当铁液中的含硫量太高时,硫与镁和稀土生成硫化物,因其密度小而上浮到铁液表面,而这些硫化物与空气中的氧发生反应生成硫,硫又回到铁液,又重复上述过程,从而降低了镁与稀土含量。当铁液中的硫大于0.1%时,即使加入多量的球化剂,也不能使石墨完全球化。 (3)稀土与镁:稀土与镁含量过低时,往往产生球化不良或球化衰退现象。一般工厂要求球化剂的加入量为1.8%~2.2%。 (4)壁厚:铸件壁太厚也容易产生球化不良及衰退缺陷,主要是因为铁液在铸型中长时间处于液态,镁蒸汽上浮,造成镁含量降低;共晶时大量石墨生成而释放出的结晶潜热使奥氏体壳重新熔化,石墨伸出壳外而畸形长大,形成非球状石墨。 (5)温度:若铁液温度过高,铁液氧化严重,由于镁与稀土易与氧化物产生还原反应,而使得镁、稀土含量降低,同时高温也将增加镁的烧损和蒸发;铁液温度太低,球化剂不能熔化和被铁液吸收,而上浮至铁液表面燃烧或被氧化。 (6)滞留时间:铁液中镁的含量是随孕育处理后停留时间的增加而减少,其主要原因是因硫及镁、稀土的氧化与蒸发造成的。一般情况下,滞留时间不超过20min。 (7)浇冒口:冒口设计是不合理的,将有施法时间太长,铁水飞溅,以及空气中的参与,因此,镁,稀土氧化物是严重的。
球墨铸铁管配件采用承口和承口衔接,钢管一般采用焊接,两管的内外径都不相同,所以它们两者的衔接操作需求特殊的办法。目前,衔接办法主要有两种,分别是法兰衔接和承插衔接。法兰衔接是一种通用的衔接办法。该办法的原理是将球墨铸铁管和钢管转换为法兰接口,实现标准对接。球墨铸铁管的标准配件有两种:盘式短管和盘式短管。管件的承口或承口可与一般管道衔接让管道可转换为法兰接口,只能衔接相应的钢法兰。这种衔接方法愈加遍及,以法兰为标准件,保证了衔接的稳定性。需求留意的是,这两个法兰不只需求相同的标称值,并且还需求PN值来衔接。球墨铸铁管适合用于自来水主管网铺设和老管改造。球墨铸铁管内外防护全是“食品级”资料,就像给供水管道上了“双保险”,保证居民供水。共铺设球墨铸铁管1630公里,占主供水管网的90%以上。一般路途下原有供水管道主要是上世纪七八十年代初铺设的灰口铸铁管和混凝土管。据介绍,这种管内壁均为铁管,老化后会呈现铁锈,易积存水垢,长期使用后管道内壁呈现不同程度的堵塞,严峻处管道口径从100毫米缩小到50至70毫米,严峻影响水压。球墨铸铁管和混凝土管脆性大、承压能力低,一旦土壤承载力发生变化,管道水泥接口极易变形,导致爆管,影响城市供水。
球墨铸铁管我们已经很了解了,一种管道,可以用在很多地方,安装球墨铸铁管可不是一个简单的活,我们需要注意很多事项,具体有哪些呢?我们可以了解一下! 1.把铸铁管口的杂物进行清理并且擦洗干净。 2.清洗胶圈和上胶圈。把胶圈上的脏东西清洗干净,并且将其弯成梅花形或者8字形装到承口槽内,并且用手沿着整个胶圈按压一遍,或者用橡皮锤砸实,以保证胶圈的各个部分不翘不扭,均匀的卡在槽内。 3.把那个插口外表面和胶圈上面弄些润滑剂,均匀的涂刷在外围。 4.将铸铁管下到槽底。 5.安装机具设备,把准备好的设备安装好,然后避免再次污染。 6.检查安装的位置是否符合要求。 球墨铸铁管配件
球墨铸铁管配件前两个主要由化学传感器检测,通常是在使用组件或系统的过程中。如果有合适的传感器,这种方法比较简单。球墨铸铁管的气密性试验需覆盖在铸铁管内。如果发生渗漏,***需要清理土壤,破坏混凝土,这将不可避免地影响工程的进度。通常我们采用以下几种方法对球墨铸铁管进行气密性检查:常用的气密性试验方法有气泡法、涂抹法、化学示踪气体检漏法、压力变化法、流动法、超声波法等。传统的泄漏检测方法是气泡法和污点法。气泡法是将工件浸入水中,用压缩空气填充,然后从中收集气泡以测量泄漏量。涂抹法是一种能在工件表面产生一定压力的肥皂、水等气泡,并观察气泡情况来检测泄漏尺寸的液体。操作简单,这两种方法可直接观察区和渗漏的情况,但因为我事先不知道工件的泄漏定位和几个泄漏,很难收集所有的气泡,影响测量的准确度;其次,对大型、笨重和复杂的部分,气泡附着零件的底和折叠,不易观察。试验结束后,对工件进行清洗干燥,不能实现自动定量检漏。